Over the years,
inventors and engineers have not been able to implement dramatic
improvements to the ignition system of an internal combustion
engine, other than increasing its longevity. The basic function
of even the latest ignition systems has remained unchanged
for over 70 years. In the combustion chamber, the net effect
is a small, stationary spark across a one millimeter gap.
In
1990, scientists from Princeton University and the Princeton
Plasma Physics Lab began to apply advances in plasma physics
to the ignition systems of internal combustion engines. After
several years of steady progress, the Princeton team demonstrated
and patented a breakthrough design called Kinetic Spark Ignition™ (KSI™).
Knite, Inc. was formed to commercialize KSI and is the sole
owner of all U.S. and international patents covering this
technology
A conventional
ignition system fires a long-lasting, stationary, high-voltage
discharge
(plasma) across the gap between the spark plug electrodes – igniting
a very small volume of the air-fuel mixture in a combustion
chamber.
The plasma “bridges” the gap but
never expands into the chamber. Once the plasma forms,
most of the current that continues to flow into it is
wasted because it doesn’t generate a greater volume
of plasma.
|
|
The KSI
system takes a different approach.
A high voltage discharge creates “seed” plasma
between two electrodes inside a spark plug of proprietary design.
This discharge acts as a switch to allow a capacitor to deliver
energy directly into the discharge, bypassing the coil. This
second pulse of low-voltage, high-current electricity “grows” the
seed plasma. KSI has a pulse duration that is much shorter
than that of a conventional ignition system. An electro-magnetic
force (known as the Lorentz Force) accelerates the plasma along
the two electrodes, “ejecting” it into the air-fuel
mixture in the combustion chamber. The patented system, coupling
a proprietary igniter and electronics, forms a large volume
of plasma that ignites a much larger portion of the air-fuel
mixture than could a conventional spark.
The conversion of electrical energy
into plasma by the KSI system is very efficient (greater
than 90%). This allows
the KSI™ system to create an accurately-timed “ignition
kernel” significantly larger than the spark of a conventional
ignition at the same level of energy consumption. The end
result is a faster, more uniform, and more complete burn
of the air/fuel
mixture.
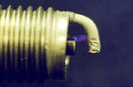 |
Using
the same energy input, a KSI™ system generates
an “ignition kernel” dramatically larger
than a conventional ignition system spark, which
produces major improvements in engine operation.
|
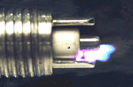 |
Conventional
Ignition
|
|
KSI Ignition
|
The KSI
system’s short pulse duration provides precise ignition
timing. It also creates an excellent opportunity for the
inclusion of ion sensing. The timing control enabled by the
precise short duration pulse also means that the engine speed
is only limited by the rate at which the ignition system
can be charged. Restrictions due to ignition discharge parameters
are eliminated with the KSI system.
The KSI
technology utilizes Lorentz force (electro-magnetic) and
thermal forces derived from the geometry of the igniter’s
electrodes and the pulse shape provided by the discharge
electronics. The resulting large ignition kernel provides
the maximum gain
in operating parameters without using excessive amounts of
ignition energy. Additionally, with Lorentz force causing
the plasma to move along the electrodes, erosion is reduced
by
having the discharge spread its energy deposition along the
surface of the electrodes.
Knite’s
Kinetic Spark Ignition™ system opens the
door to solving engine performance problems that were once
considered impractical or impossible with conventional
ignition technologies. KSI™ enables engines to run
better on a wide variety of fuels, with higher compression
ratios, increased
EGR (Exhaust Gas Recirculation), and ultra-lean fuel mixtures.
As an enabling technology, KSI can simplify the integration
and enhance the performance of other advanced engine technologies,
such as GDI (Gasoline Direct Injection).